Which is better, a cone crusher or a jaw crusher?
Jaw crushers and cone crushers are vital in the crushing industry, with jaw crushers excelling in primary crushing of wet, sticky materials and cone crushers in secondary crushing, offering higher capacity, finer output, and better grain shape. Selection depends on material, production scale, and budget.
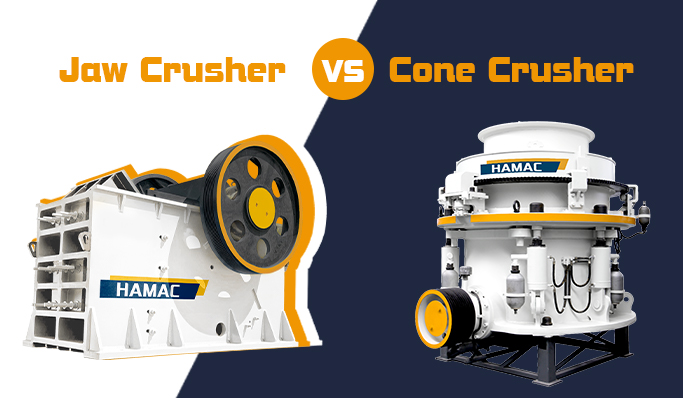
Below is a detailed comparison of their working principles, material handling capabilities, and applications.
Working principles
In a cone crusher, the driving shaft rotates the crushing cone, which compresses materials against the fixed outer walls. Crushed materials slide down from the machine's sides until they are small enough to exit through the bottom.
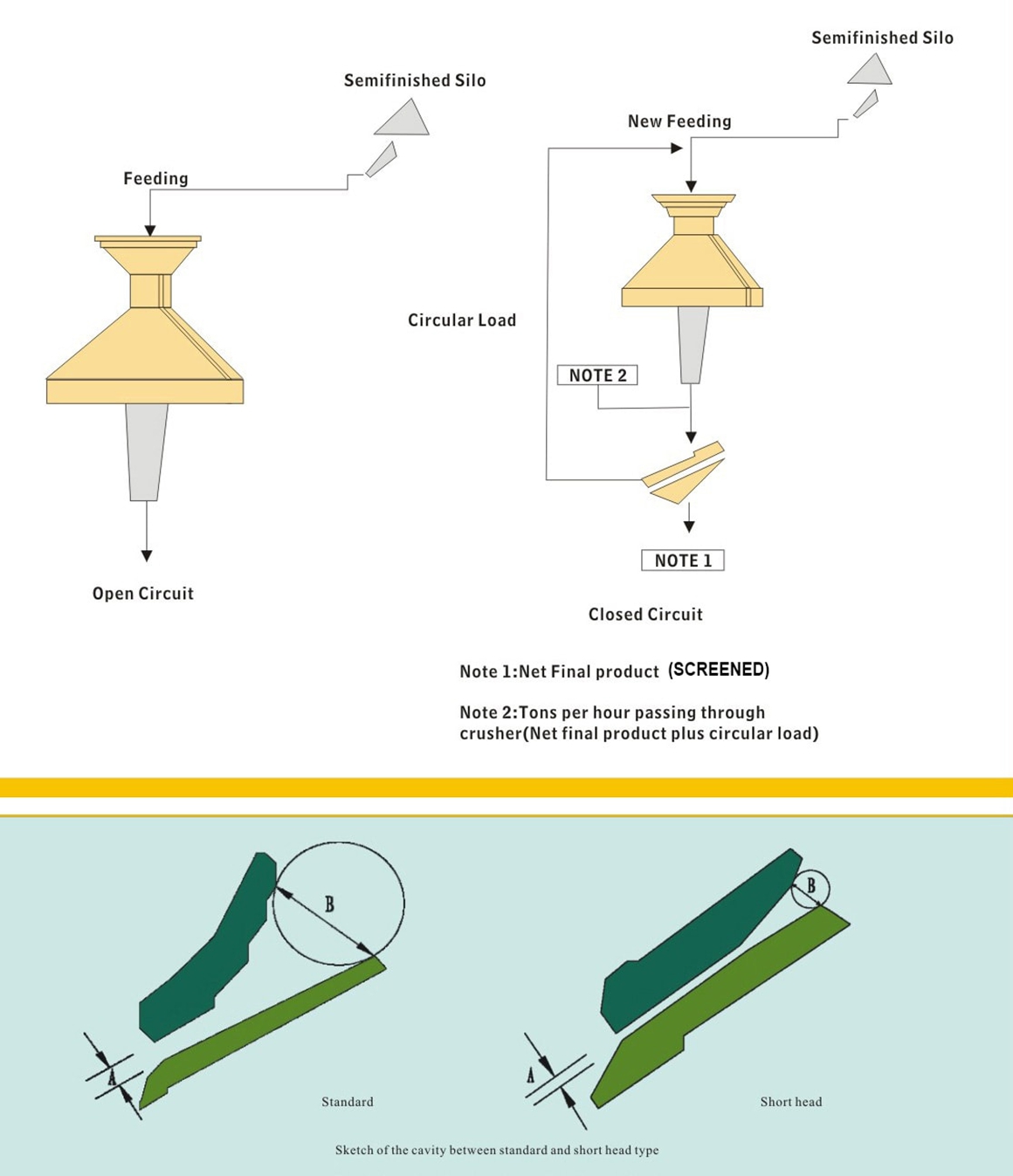
A jaw crusher operates by repeatedly compressing materials between a fixed jaw plate and a moving jaw plate. As the movable jaw plate presses the material against the fixed plate, it breaks into smaller pieces. When the movable plate retracts, the crushed material slides down the crushing chamber and exits.
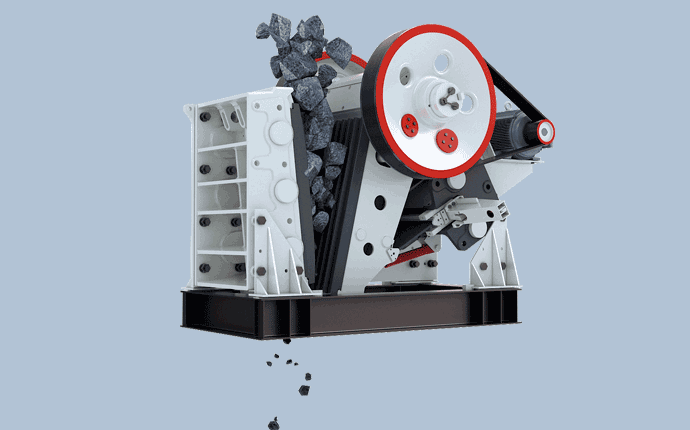
Material handling
Cone crushers are more versatile in handling materials. They allow for direct feeding until the chamber is fully loaded, maximizing their operational efficiency. This makes cone crushers particularly well-suited for high-capacity operations and large-scale production lines, where consistent throughput and minimal downtime are critical.
The jaw crusher, on the other hand, is ideal for processing sticky materials with high moisture content due to its simple structure and crushing mechanism. However, feeding the jaw crusher requires attention; the material must be evenly distributed, and the chamber should not be overloaded, with its volume kept below two-thirds of its height to ensure efficient operation and prevent blockages.
Applications
Both jaw crushers and cone crushers play essential roles in material processing, but they are typically used at different stages of production due to their distinct designs and functionalities.
Jaw crushers are most commonly used as primary crushers. Their robust design and powerful crushing mechanism make them suitable for reducing large, raw materials like rocks, ores, and other bulky materials into smaller, more manageable sizes. These smaller fragments are then easier to transport and process in subsequent stages of production.
Cone crushers, by contrast, are typically employed as secondary or tertiary crushers. They take the material processed by the jaw crusher and refine it further, breaking it down into finer, more precise sizes that meet specific requirements for particular applications. Additionally, cone crushers are often chosen when high-quality grain shape, such as cubic or uniform output, is desired, making them indispensable in industries like construction, road building, and aggregate production.
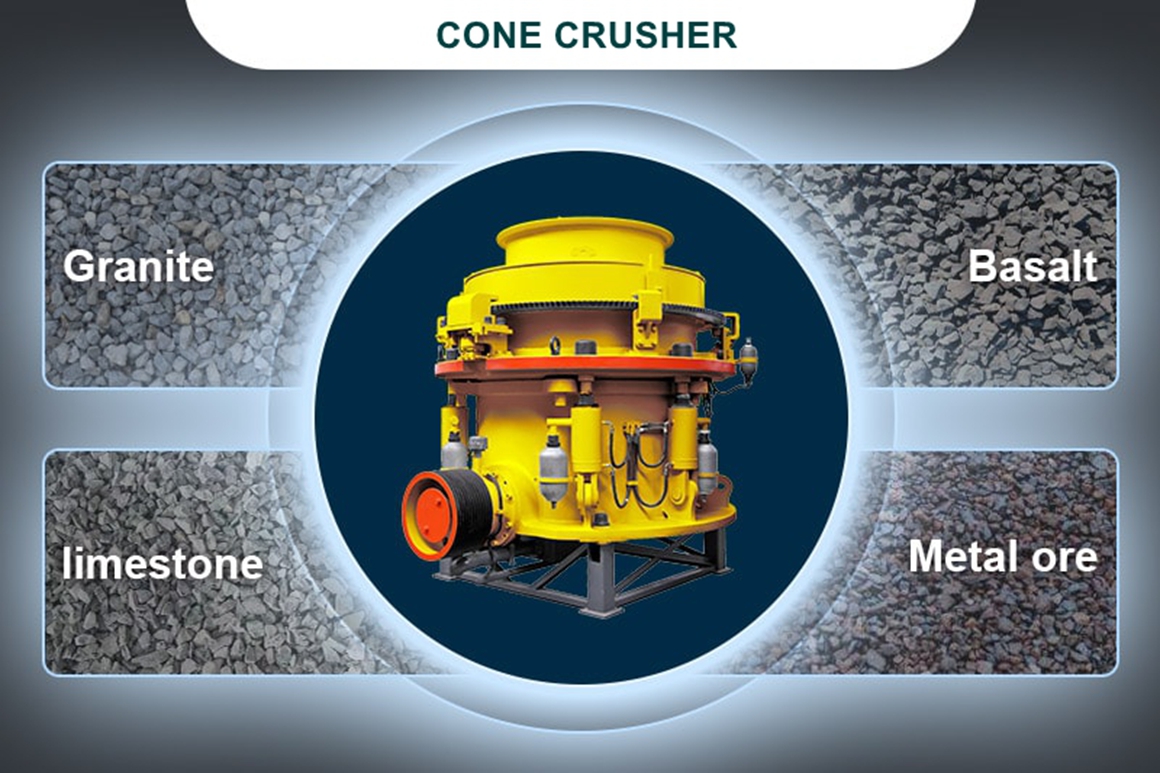
Different grain shape
Cone crushers typically produce better grain shapes compared to jaw crushers. When using a jaw crusher, additional shaping equipment is often required to achieve an improved grain shape. Cone crushers, on the other hand, can serve both crushing and shaping purposes due to their lamination crushing principle, which results in final products with a desirable cubical shape.
Differences in maintenance costs
Regular maintenance is essential during crusher operation. While the initial investment for a cone crusher is higher, it offers a lower failure rate during production, a longer replacement cycle for wear parts, and more convenient maintenance and repairs. This ultimately reduces the need for extensive manpower and resources, leading to long-term cost savings.
After comparing the two, we can identify the differences between jaw crushers and cone crushers. When selecting the right crusher, consider the following factors. First of all, investment cost. If both jaw and cone crushers meet your production needs, opt for the jaw crusher as it is more cost-effective. Secondly, production scale. For large-scale production lines, a cone crusher is the better choice due to its efficiency and capacity. What's more, you should consider the material characteristics. For wet, cohesive ores, a jaw crusher is more suitable. For hard, flaky, or elongated ores, the cone crusher is recommended.
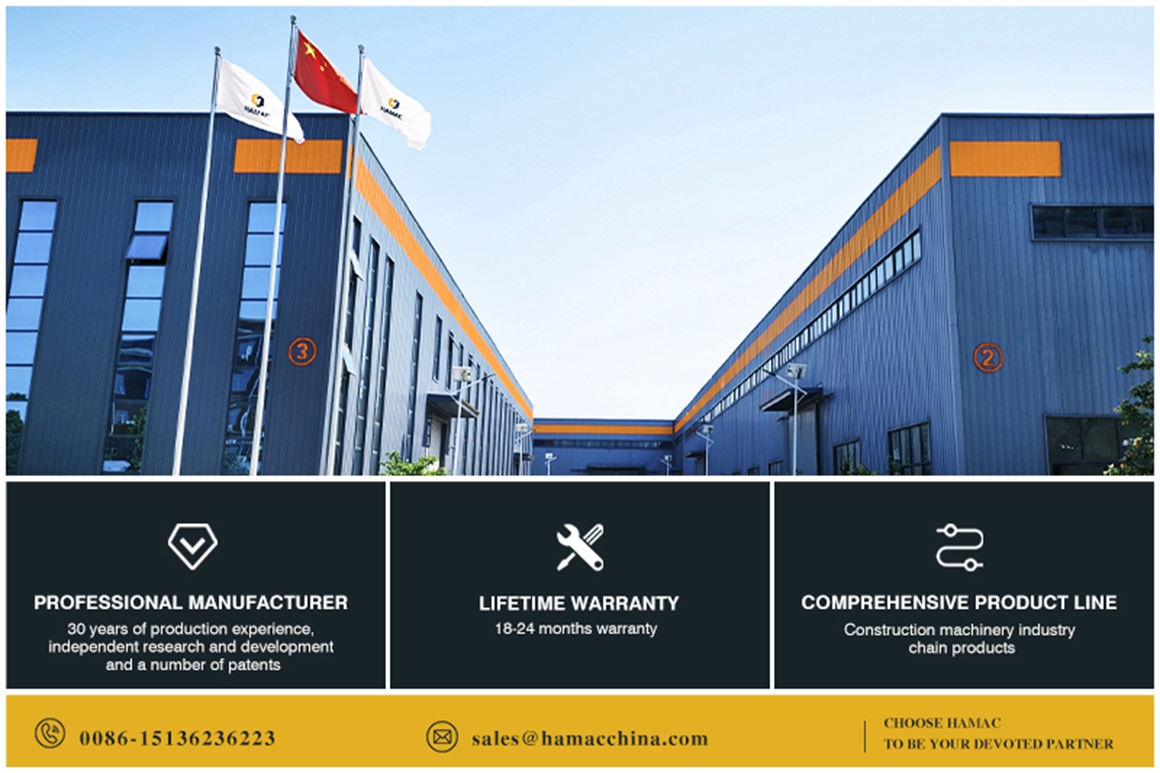
If you're unsure which crusher suits your needs, consult HAMAC engineers. Based on your specific requirements and production goals, we'll recommend the most suitable jaw or cone crusher for your operation.