What is the difference between jaw crushers and impact crushers?
Jaw crushers and impact crushers are essential crushing equipment in mining, construction, and other industries. For newcomers to this field, distinguishing between the two can be challenging. Below are the main differences between jaw crushers and impact crushers, focusing on their practical applications.
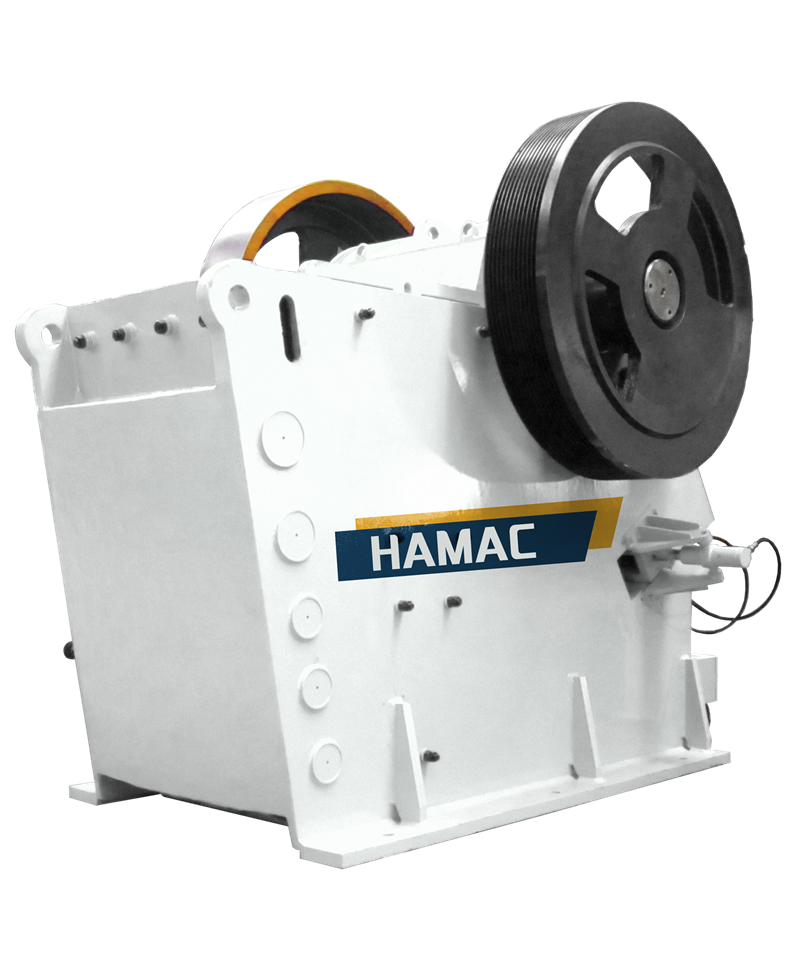
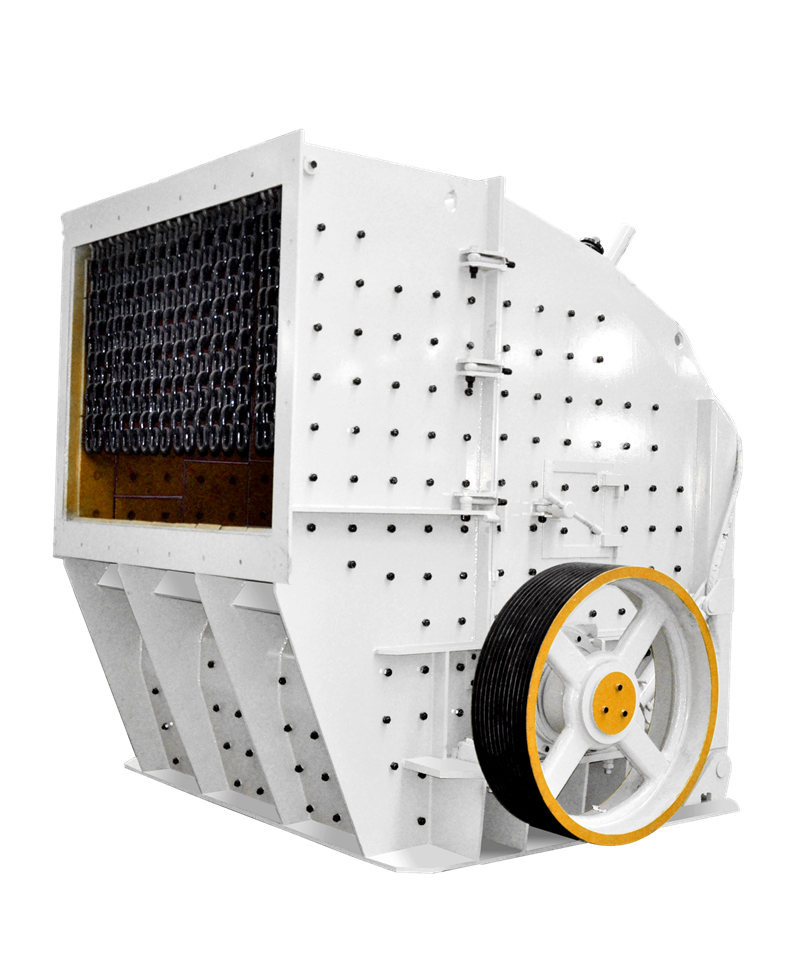
1. Application scope
Material hardness
The jaw crushers are suitable for crushing a wide range of materials, from soft to very hard, with compressive strength up to 300-350mpa. These machineries are versatile and come in coarse and fine variations, making them ideal for primary crushing tasks. While the impact crushers are best for medium to soft materials like limestone. Hard materials can significantly wear down impact crushers, reducing the service life of key components. Impact crushers excel in coarse, medium, and fine crushing and allow flexible adjustment of the discharge size to meet diverse requirements.
Material size
A jaw crusher is primarily used for large materials up to 1200mm (depending on the model). Commonly employed in mining operations and sand production. Nevertheless, an impact crusher is typically used for medium to smaller materials, making it better suited for secondary processing.
2. Structure and working principle
The jaw crusher operates using a compressive, curved extrusion mechanism, where materials are crushed within a chamber formed by a fixed jaw and a moving jaw.
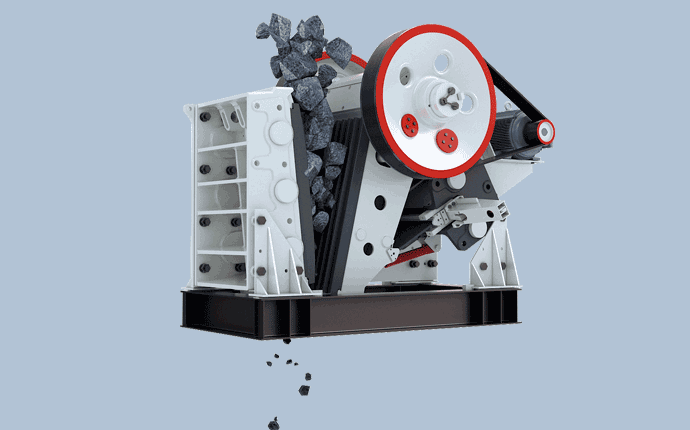
In contrast, the impact crusher relies on an impact mechanism, where materials are repeatedly struck and broken between a ratating rotor, equipped with plate hammers, and a stationary impact plate.
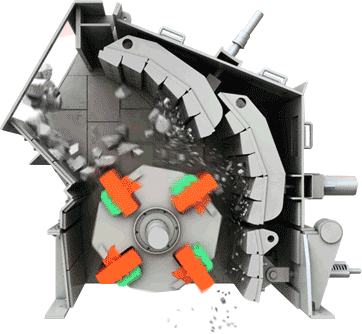
3. Roles in the production line
The jaw crusher serves as a primary crushing machine and is an essential component in various production lines, including sand-making, aggregate production, and mineral beneficiation. Its robust design and high crushing capacity make it ideal for handling large and hard materials, ensuring the initial size reduction needed for further processing.
On the other hand, the impact crusher is primarily used as secondary or tertiary crushing equipment, designed to produce finer material sizes for applications such as concrete and asphalt production. Its ability to deliver precise and consistent particle sizes makes it highly effective for refining materials. Additionally, for softer or less abrasive materials like limestone or gypsum, the impact crusher can also serve as a primary crusher, offering flexibility in production line design and reducing the need for multiple stages of crushing.
4. Production capacity
Both jaw and impact crushers are available in a wide range of models, designed to accommodate varying production requirements. Jaw crushers are typically used for primary crushing, offering high throughput and consistent performance, making them ideal for handling large volumes of material.
Impact crushers, on the other hand, are more versatile and can handle both primary and secondary crushing, with models tailored for medium to high production demands. The choice of crusher model depends on factors such as the type of material, desired output size, and overall production goals.
5. Discharge fineness
The discharge fineness of a jaw crusher is typically coarser, with output sizes generally around 300-350mm, depending on the specific model. On the other hand, an impact crusher is designed to produce finer output sizes, making it suitable for medium and fine crushing applications. The exact discharge size for both crushers may vary depending on the properties of the processed materials.
6. Grain shape
The jaw crusher generally produces output with a higher proportion of needle-shaped and elongated particles. While this is suitable for many applications, it may not meet the demands of projects that require uniform particle shapes, such as concrete production or road construction, where consistent quality and strength are essential.
In contrast, the impact crusher is designed to deliver more uniform, cubical particle shapes with fewer sharp edges. This feature makes it particularly effective for shaping materials, enhancing their quality and usability in applications requiring smooth, well-graded aggregates. In production lines, the impact crusher is often used after a jaw crusher to refine the output, ensuring a higher-quality product suitable for use in industries like asphalt production, concrete mixing, and decorative aggregates.
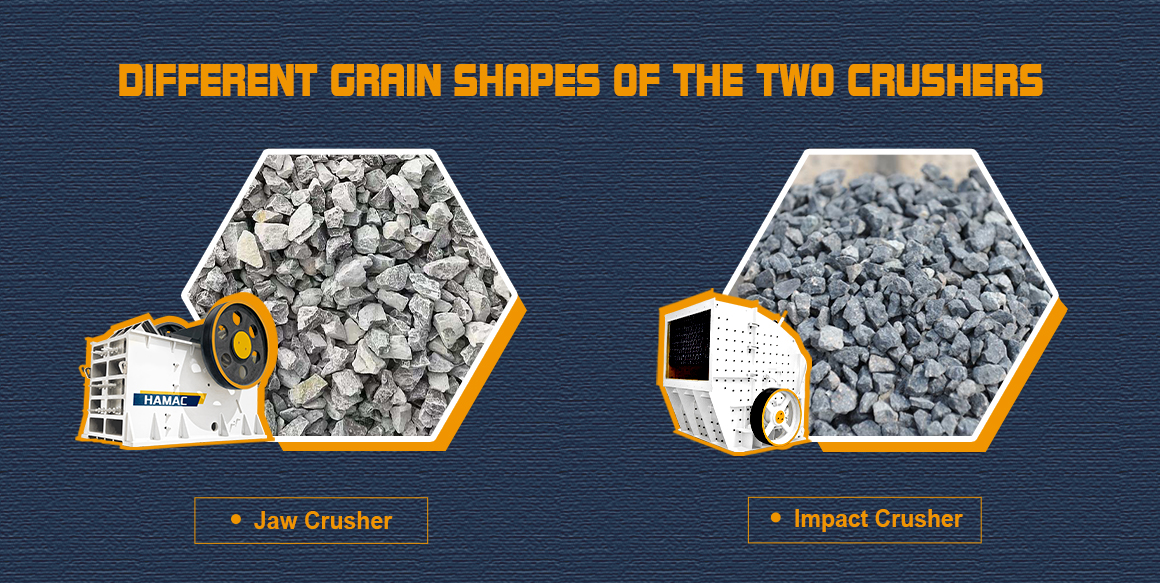
7. Price and cost-effectiveness
The jaw crusher is typically more affordable, owing to its traditional and straightforward design, as well as lower production and maintenance costs. Its reliability, efficiency, and relatively low power consumption make it a highly cost-effective option for primary crushing, particularly for operations focused on durability and long-term savings.
In comparison, the impact crusher is usually priced higher due to its more advanced design and additional capabilities, such as producing finer and more uniform outputs. Its ability to shape materials and handle secondary or tertiary crushing requirements adds significant value, especially for projects requiring precise particle sizes or high-quality end products. While it involves a higher initial investment, its versatility and performance can offer long-term benefits for specific applications.
Selecting the right crushing equipment depends on your specific production needs. Jaw crushers are ideal for coarse crushing of a wide range of materials, while impact crushers excel in secondary or fine crushing with superior grain shape. For expert guidance and customized solutions, consult HAMAC’s professional engineers to help design the most efficient production line for your requirements.